This website uses cookies so that we can provide you with the best user experience possible. Cookie information is stored in your browser and performs functions such as recognising you when you return to our website and helping our team to understand which sections of the website you find most interesting and useful.
A wide range of products
Our plant produces a whole range of furniture elements that we deliver to our partners in Poland and Europe. We produce furniture fronts in many variants, furniture boards, table tops and finishing strips, furniture bodies, wardrobe doors and even panels for residential doors. All these elements are used to create kitchen, room, bathroom, children’s, bedroom and office furniture. Such a wide range of choices requires the use of appropriate solutions and reaching for proven materials that will ensure durability in any type of room.
The production is based on wood-like materials: chipboards and MDF boards with a reduced formaldehyde content and meeting strict international standards. In addition, the raw material used in production comes from a certified supply chain, and we as a company follow good practices related to the protection of forest management, which is confirmed by the FSC® certificate that applies to all our products. We finish the surface of the boards with high-quality foils and various colours and patterns. These are PVC, PET, PP, and ABS / ACRYLIC films.
In production processes, we use such modern and reliable solutions as:
- vacuum pressing technology,
- HOT MELT LAMINATION technology used in the production of furniture boards and ribbons,
- a method of continuous coating of narrow elements used for the production of finishing strips,
- CNC machining,
- the MICRO MILLING™, the technology of finishing furniture board,
- FLICK&CLICK™ toolless mounting system.
Find out more about our technologies and learn about their benefits for furniture manufacturers.
Vacuum pressing technology
Vacuum pressing is a technology that we use to create furniture elements MELAFOL and MAGIC GLOSS . It provides the perfect finish for three-dimensional fronts and furniture elements. In this process, a thermoplastic film (PVC, PP, PET) is applied to the MDF board, which is formed by creating a vacuum between it and the board. The great advantage of this technology is the ability to precisely cover the component in three dimensions (3D) with foil. The resulting element is extremely durable and very easy to care for.
The vacuum technology is also great for the production of fronts finished with the demanding PREMIER MATT foil, which gives the furniture elements a deep matt effect. In combination with the innovative PST (Physical Surface Treatment) technology, PREMIER MATT furniture fronts are not only durable and resistant to moisture or elevated temperatures. Their surface can be easily “healed” with heat.
You can read more about it in the post: Vacuum technology in the production of PREMIER MATT fronts. Discover a solution that combines modernity and functionality.
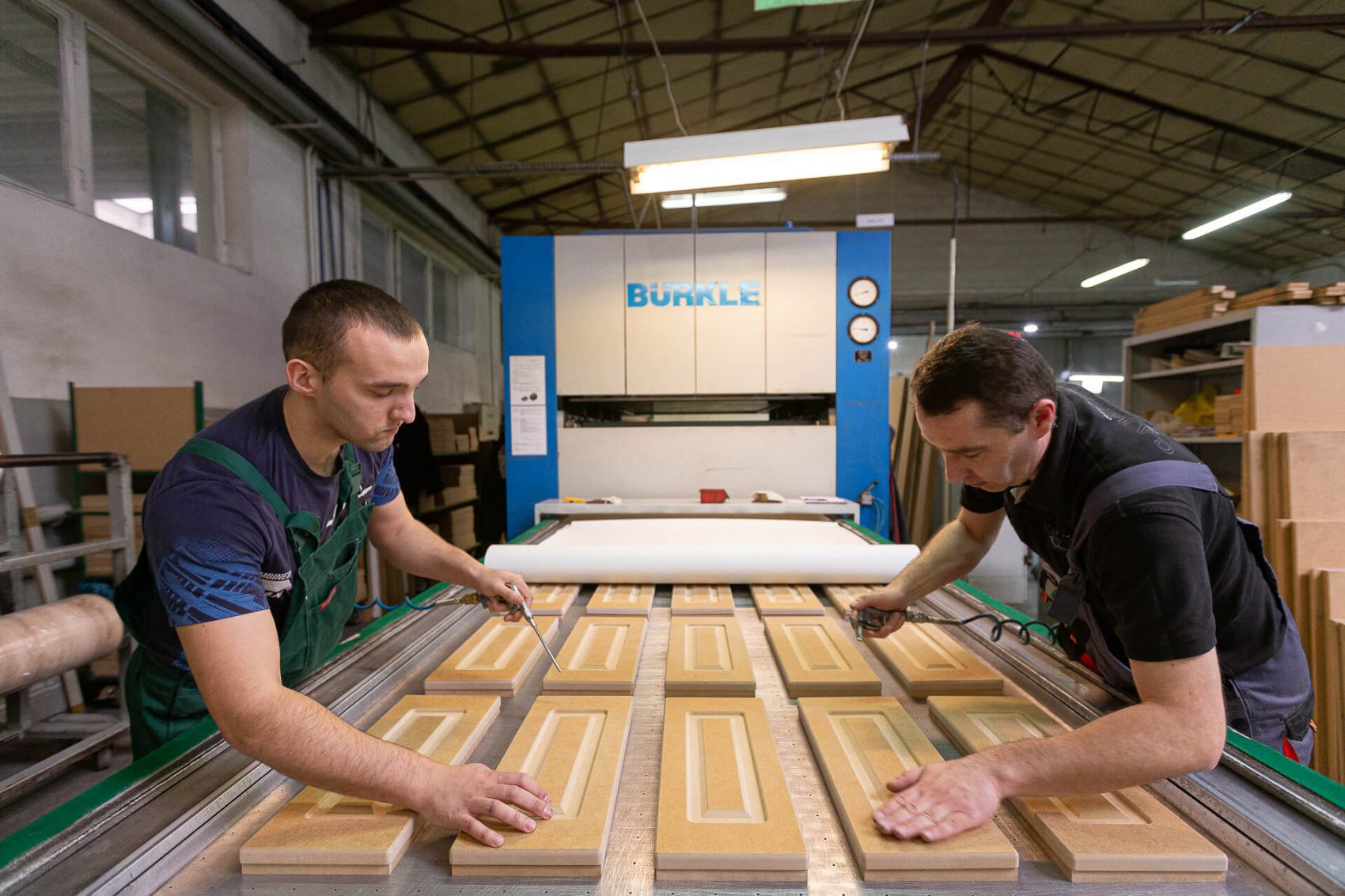
HOT MELT LAMINATION
The continuous lamination technology is considered to be one of the most modern production processes. It provides excellent quality of the finished surface and is widely used in our plant in the production of COMPLETE SKIN furniture boards and ribbons. During the process, the PUR reactive adhesive is evenly applied to the chipboard or MDF and immediately covered with a polymer film of PVC, PP, PET or a FINISH film. As a result, the component is distinguished by a perfectly finished surface, and the adhesive joint is highly resistant to moisture and elevated temperature.
You can read more about it in the post: COMPLETE SKIN boards and ribbons. What does the production process look like? In the text, we present the technologies that are involved in the production of furniture boards and ribbons, as well as reveal how furniture ribbons with a profiled POSTFORMING edge are made. In our factory, we use edges with radii from R2 to R65 mm.
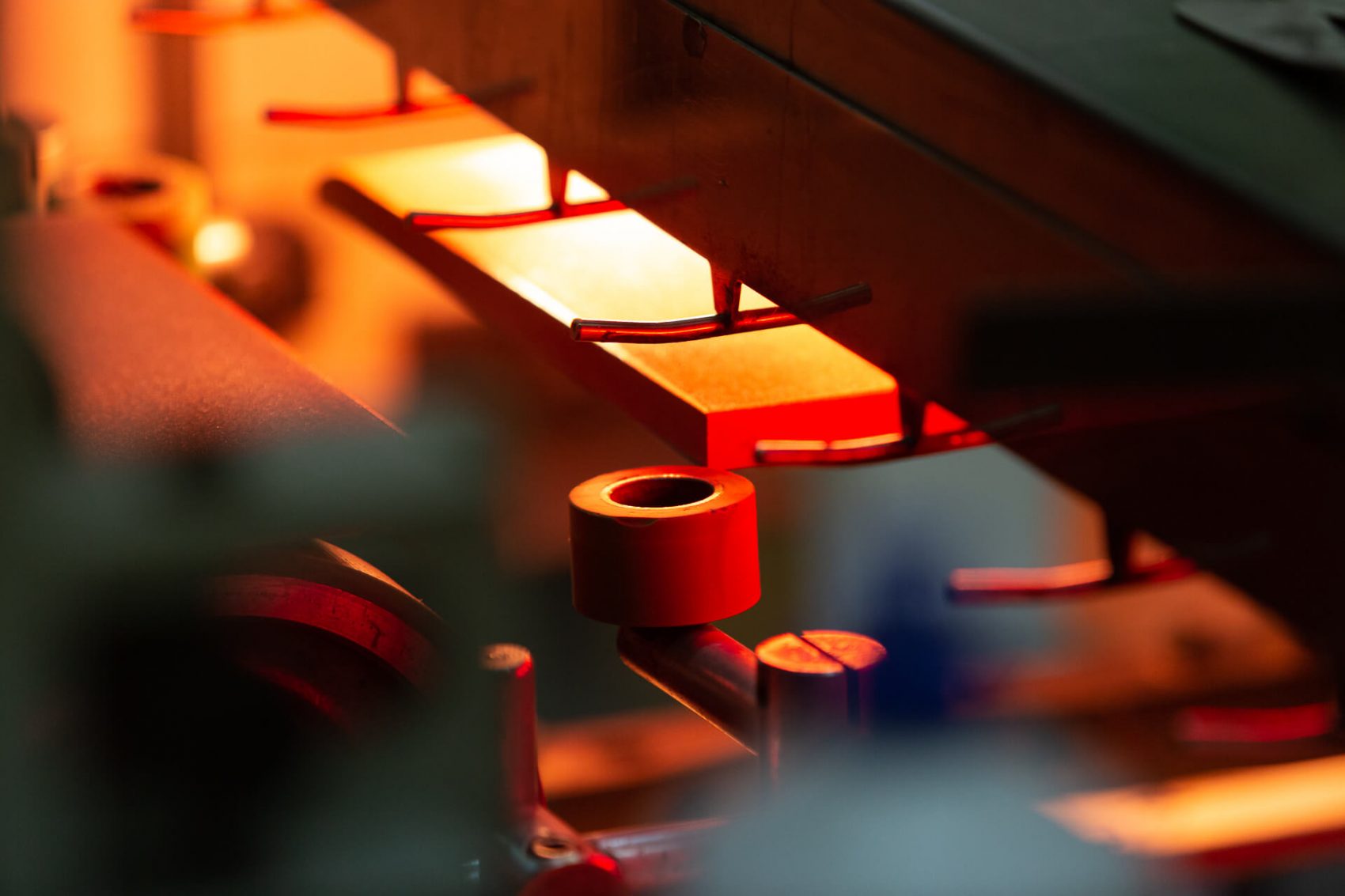
Continuous coating of narrow elements
We use the continuous coating process for the production of strips, profiles and panels. In production, we use MDF boards or chipboards with FSC® certificate and reduced formaldehyde content. We also use plywood and solid wood glueing. On its surface, we apply a PVC, PP or PET polymer film with a thickness of 0.1-0.4 mm and a FINISH film.
How exactly are strips, profiles and panels made in the continuous coating technology and what are their applications? Read the entry Finishing furniture strips – production and application, in which we present ready-made solutions for furniture manufacturers.
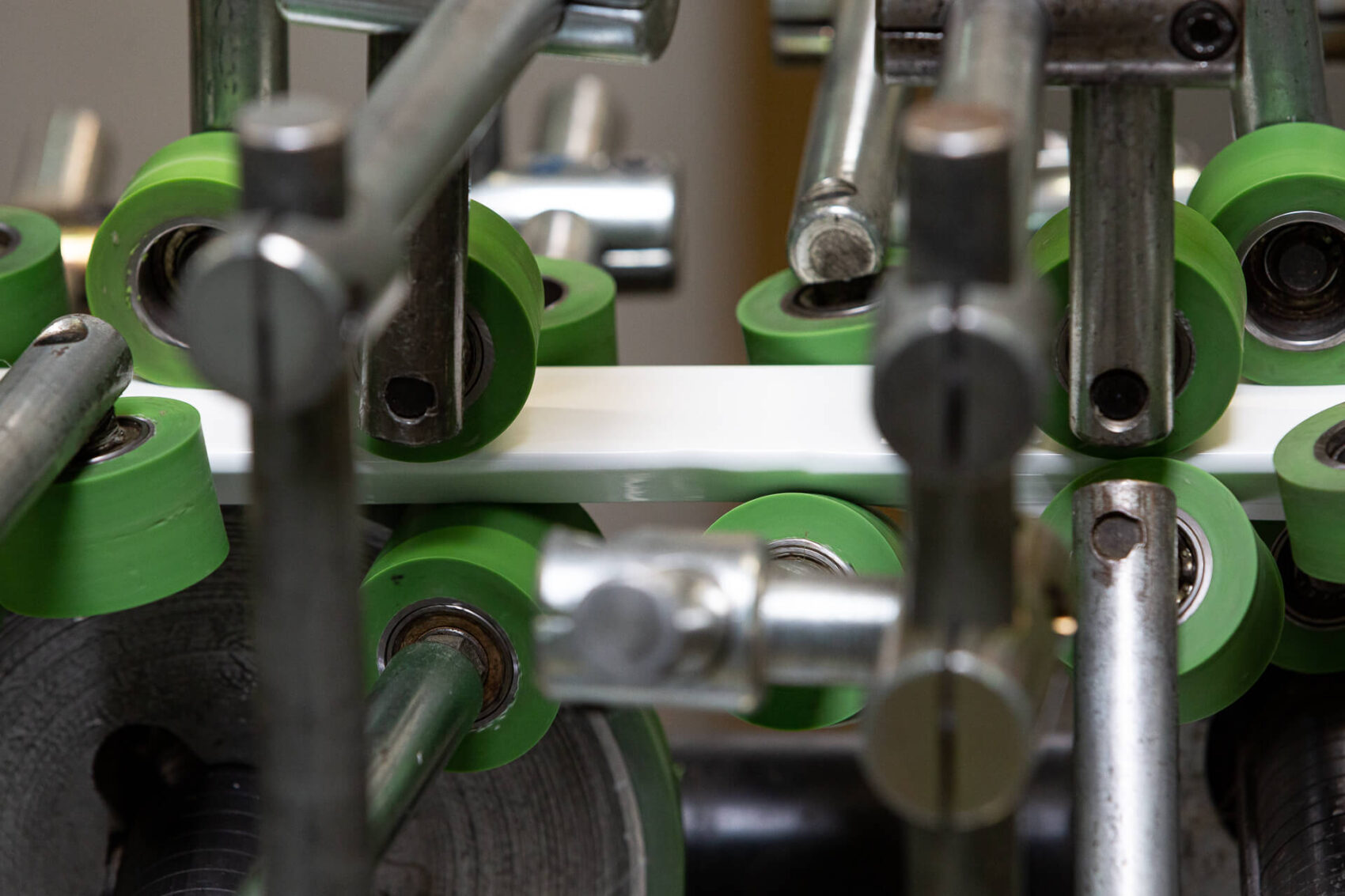
CNC machining
Modern machining and drilling centres using CNC technology enable us to carry out such processes as milling, drilling or rebating. We are able to mass-produce elements of any finish, equipped with drilling for assembly, as well as free cutting and processing of boards. All with the highest precision and high repeatability, which reduces production errors to a minimum.

MICRO MILLING™
The MICRO MILLING™ technology consists of precise surface treatment of the COMPLETE SKIN plate, which is covered with a two-colour foil with a thickness of 200 μm to 300 μm, and then subjected to a precise milling process with real-time electronic copying of the surface in the thickness range of 50 μm-100 μm. The effect obtained in this way is very popular among manufacturers who like to give their furniture collections a unique character.
In the MICRO MILLING™ technology, we use specialized Alphacam software, which enables the import and processing of even the most complex graphic designs into machine codes. This means that we are able to implement almost any pattern.
You can learn more about the advantages of fronts in this technology in the post: MICRO MILLING™ – the new version of furniture fronts.
System FLICK&CLICK™
The Flick&Click™ system based on the Threespine® toolless assembly is a technology that we are constantly developing. It is very popular, especially among manufacturers looking for innovative solutions for their products. Its greatest advantage is undoubtedly the method of assembly – you do not need screws, dowels or tools to assemble the furniture. Thanks to this, there are no visible connections or cuts on the surface of the furniture that could disturb its aesthetic appearance.
The FLICK&CLICK™ system offers two types of connection: symmetrical M45 connection and asymmetrical CORNER90 connection, also ensuring tool-free disassembly. Find out more about both solutions, their advantages and application: Flick&Click™ M45 vs CORNER 90 – technological possibilities of both solutions for furniture manufacturers .
The production of furniture elements in the FLICK&CLICK™ system enables us to carry out interesting orders for our partners. We use this technology to implement standard projects, such as modular bathroom furniture, the production of which we described on our blog: An example of implementation in the Flick&Click™ system: Furniture modules for the bathroom. There are also challenges, for example, related to the type of raw material used in production, such as in the case of the innovative DYI furniture collection, which we have realized for a Swedish manufacturer: DIY kitchen furniture based on a blockboard. How we implemented atypical production for the client. Contact with this technology allows us to develop our production capabilities and provides our partners with an innovative solution on a global scale.
Technologies in harmony with nature
However, modern technologies and high-quality materials are not everything. At MELACO, we also place great emphasis on the protection of the natural environment. This is confirmed by the FSC® certificate mentioned at the beginning of the article, but not only. The implemented program for the recovery of raw materials and the recycling of unused post-production waste allows us to implement the assumptions of the EU “Green Deal”. Thanks to this, cooperation with MELACO enables producers and distributors to implement their own pro-ecological strategies.
Exactly what initiatives are we taking to take care of nature? Read in the post: European Green New Deal in Melaco – how we care for the environment.
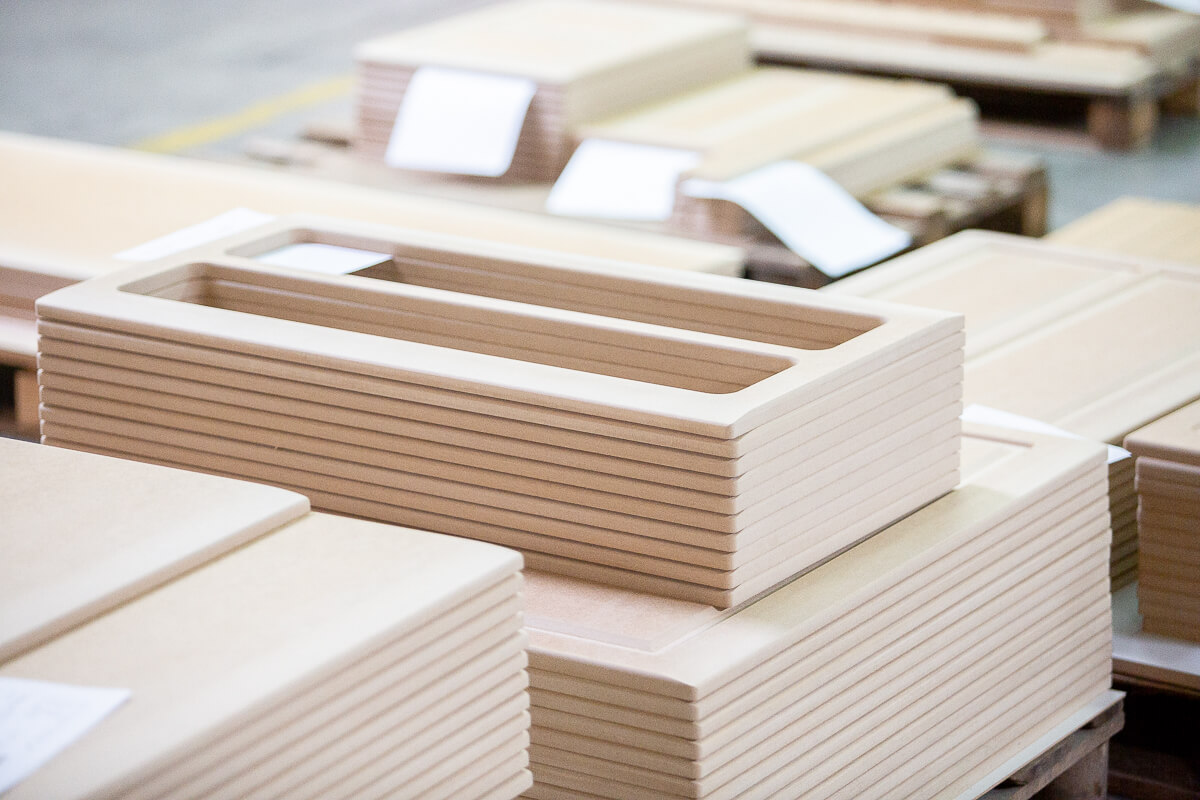
Become our partner!
Our technologies are at your disposal. Do you want to use ready-made solutions? Or do you have an idea for a completely new collection and are you looking for a contractor who will support you technically? Contact us and learn more about our technologies:
Contact
Do you have questions? Contact us.
We will be pleased to answer all questions about MELACO’s offer, terms of cooperation and orders. Write or call us.
Contact
Melaco sp. z o.o.
ul. Ciepielowska 9
67-100 Nowa Sól
Poland
SALES DEPARTMENT
Agata Sroczyńska
Sales Coordinator
SALES DEPARTMENT
Beata Prałat
Sales Specialist