This website uses cookies so that we can provide you with the best user experience possible. Cookie information is stored in your browser and performs functions such as recognising you when you return to our website and helping our team to understand which sections of the website you find most interesting and useful.
Our technologies: MICRO MILLING™
Melaco’s innovative MICRO MILLING™ technology brings a new quality to interior woodwork. If you are looking for a way to create furniture that is not only functional, but also unique and perfectly tailored to your designs, this technology is the answer. It allows any furniture manufacturer to create the most complex and original designs.
MICRO MILLING™ technology is based on the precise machining of the surface of furniture fronts covered with polymer foil. The fronts are made of Melaco’s COMPLETE SKIN furniture panel, described below. The processing consists of micro-milling the outer layer of the film, which allows for attractive visual effects. Thanks to advanced high-precision aggregates and specialised software, it is possible to reproduce accurately various motifs, from simple lines to more complex ornaments. In the production process, we use polymer films from the MELACO production range and, on special request, we can use other colours specified by the customer, allowing the product to be fully personalised.
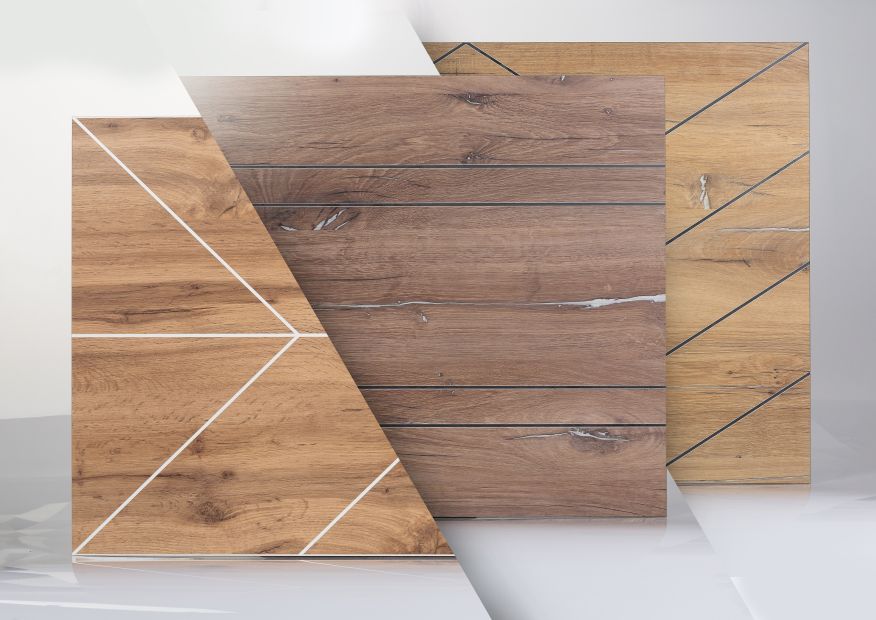
Furniture fronts with MICRO MILLING™ technology therefore feature decorations in two selected colours. In this way, it is possible to combine a favourite wood grain with, for example, black milling. The products also feature high resistance to moisture and temperature and are easy to clean, which will certainly be appreciated by future furniture users. In addition, the technology is not only used for fronts, but also for decorative panels, wardrobe doors, table tops and many other interior applications.
What are the benefits of this technology for furniture manufacturers? MICRO MILLING™ offers a low product cost compared to fronts manufactured on black coloured MDF while maintaining high strength parameters. You can read more about this in the article: MICRO MILLING™ lamellar fronts vs. solid coloured MDF base →.
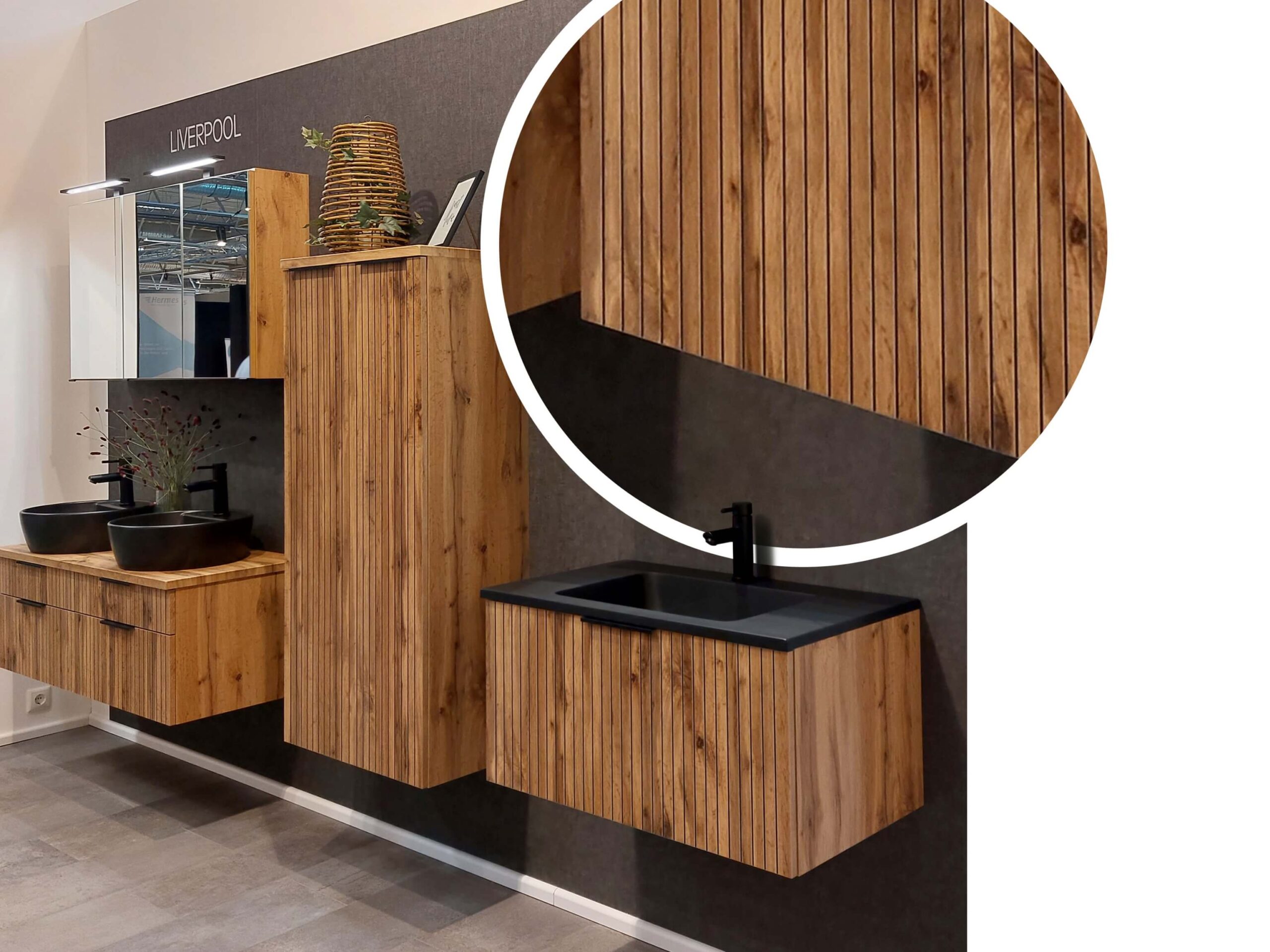
Our technologies: Flick&Click™ System
The Flick&Click™ system is based on the patented tool-free Threespine® assembly technology. Its secret lies in the simplicity of assembly, which allows furniture to be assembled without screws, dowels or other tools. There are no visible joints or holes to detract from the aesthetics of the finished product.
The Flick&Click™ system ensures an extremely precise and perfectly fitting connection of the components. The edges of the joint can be finished with a polymer edge, depending on the standard design. Depending on the material used (wood-based panels, plywood, glulam, plastic, laminate), the surface of the elements can be given a different appearance – from matt and super-matt to high gloss.
We offer two versions of the Flick&Click™ system:
Find out more about the revolutionary Flick&Click™ connections in the M45 and CORNER90 versions here: Tool-free Flick&Click™ furniture assembly: CORNER90 vs M45 →. Contact us – we will help you choose the one that works best for your furniture collections.
Our technology: Vacuum pressing
Vacuum pressing technology plays a key role in the production of fronts and furniture elements in the MELAFOL collection. It provides the ideal finish for three-dimensional fronts and furniture elements. In this process, a thermoplastic film (PVC, PP, PET) is applied to the MDF board and a vacuum is created between the film and the board. The great advantage of this technology is that the component can be precisely covered with the film in three dimensions (3D). The resulting component is extremely durable and easy to maintain.
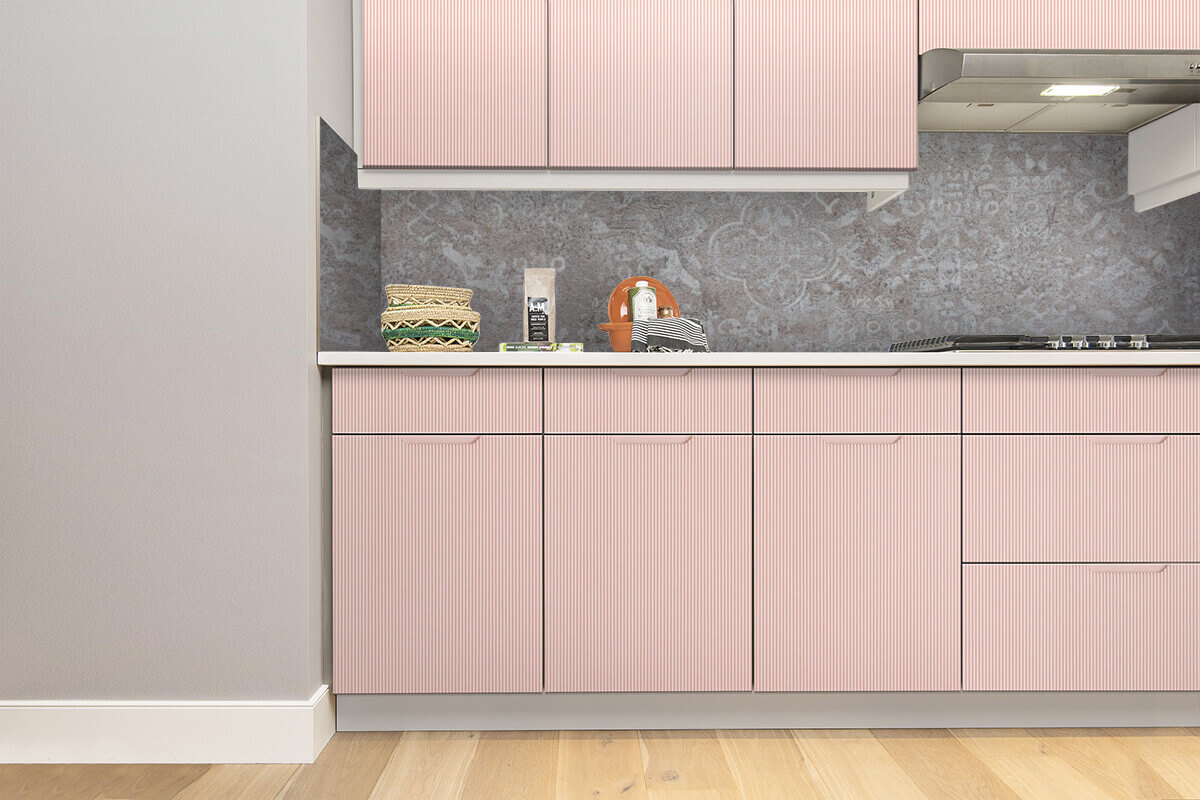
Our advanced machining centres allow us to precisely mill, drill and rebate components to ensure the highest quality finish. We work on CNC machining centres and CNC drilling centres with the possibility of machining two components simultaneously, which increases the efficiency of the process and ensures a perfect product finish in three planes. The parameters of the production process are controlled at every stage and the materials and technologies used guarantee that the high requirements are met, including heat resistance (min. 70°C). The MDF boards, adhesives and foils used in the production process have all the necessary attestations and certificates recognised both in Poland and abroad.
Pictured below from the left:
1. Wenga Flow | Toffee Premier Matt
2. Wave + Ramka | Ceramic Red
MELAFOL 3D furniture fronts and elements made using this technology offer a wide range of decorative possibilities in furniture production. Thanks to them, any furniture manufacturer can create furniture with fronts with the most refined appearance and an interesting three-dimensional effect. Geometric patterns, wavy reliefs or honeycomb structures – the possibilities are endless. Combined with a wide range of colours and motifs, MELAFOL fronts offer enormous design possibilities.
One of our bestsellers, produced on our CNC machining centres, is the Wave + Kalcite handleless fronts in various colours, shown below:
Find out more about our MELAFOL front panels and get inspired by our new products →
Our technologies: COMPLETE SKIN furniture panels
COMPLETE SKIN furniture panels are the basis for our unique products. They are exceptionally durable and versatile, offering furniture manufacturers high quality to satisfy their customers.
COMPLETE SKIN panels are made from the highest quality MDF, particle board and polymer film from leading manufacturers. Our furniture components are manufactured using advanced HOT MELT LAMINATION veneering technology with innovative PUR adhesives.
In this state-of-the-art technology, PUR reactive adhesive is evenly applied to chipboard or MDF and then coated with a polymer film (PVC, PP, PET). The result of this bonding process is not only a perfectly finished surface of the furniture components, but also a durable joint that is resistant to moisture and high temperatures. All this means that COMPLETE SKIN furniture components can also be used to make furniture for such demanding rooms as the kitchen or bathroom.
The processes available to Melaco also allow the edges of the components to be finished on one or both sides using POSTFORMING technology, giving the edges of the panel an elegant finish without a visible joint. What sets us apart from the competition is that our advanced technology allows us to finish narrow, elongated edges at the same time. This gives an elegant finish to the board without a visible joint. We also offer many types of edge profiling.
And these are just some of the benefits of our COMPLETE SKIN products. Find out more about our sheets and foils and our service of delivering finished sheets directly to your production line: Reliable Solutions for Manufacturers. COMPLETE SKIN furniture panels →
Contact
Do you have questions? Contact us.
We will be pleased to answer all questions about MELACO’s offer, terms of cooperation and orders. Write or call us.
Contact
Melaco sp. z o.o.
ul. Ciepielowska 9
67-100 Nowa Sól
Poland
SALES DEPARTMENT
Agata Sroczyńska
Sales Coordinator
SALES DEPARTMENT
Beata Prałat
Sales Specialist